Injection Molding Services
Frigate specializes in creating highly customized, on-demand prototype or production molds tailored to a diverse array of industries, from automotive to medical devices. Our offerings include a wide selection of materials, polishes, surface textures, and colors, ensuring your components meet both functional and aesthetic requirements.
What We Do
Our Injection Molding Offerings
Our experienced engineers build custom molds tailored to your specific needs. We offer various molding options to suit your project requirements.
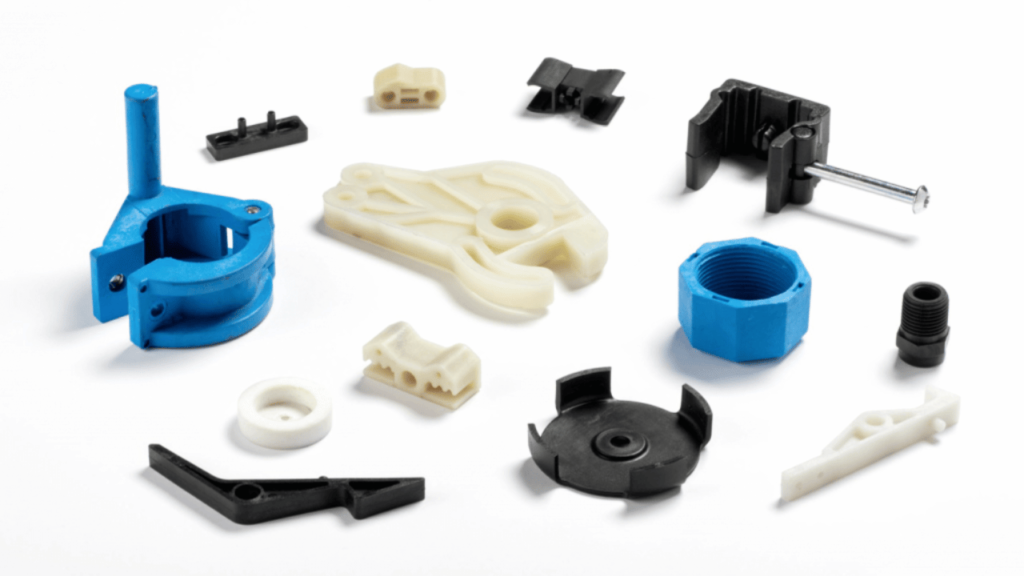
HDPE Injection Molding
Frigate specializes in providing top-notch HDPE injection molding services, ensuring superior quality and precision for your manufacturing needs. HDPE is a popular choice for injection molding due to its excellent processability, low moisture absorption rate, and lightweight properties.
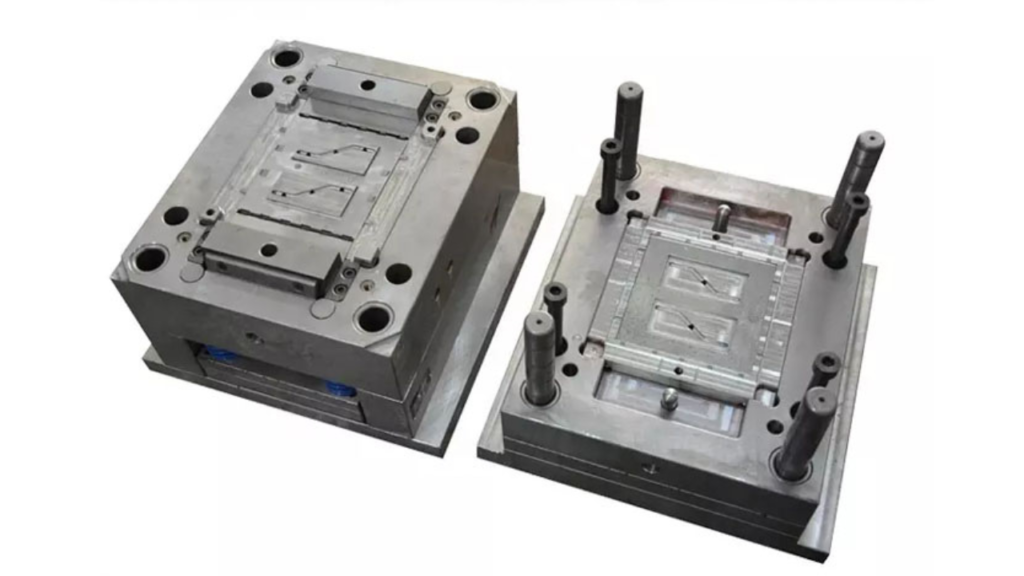
Quick-Turn Molding
Ideal for situations where fast parts are needed, such as for functional testing or low-volume production runs. These molds, typically made from aluminum for quicker turnaround, provide a cost-effective solution for rapid prototyping.
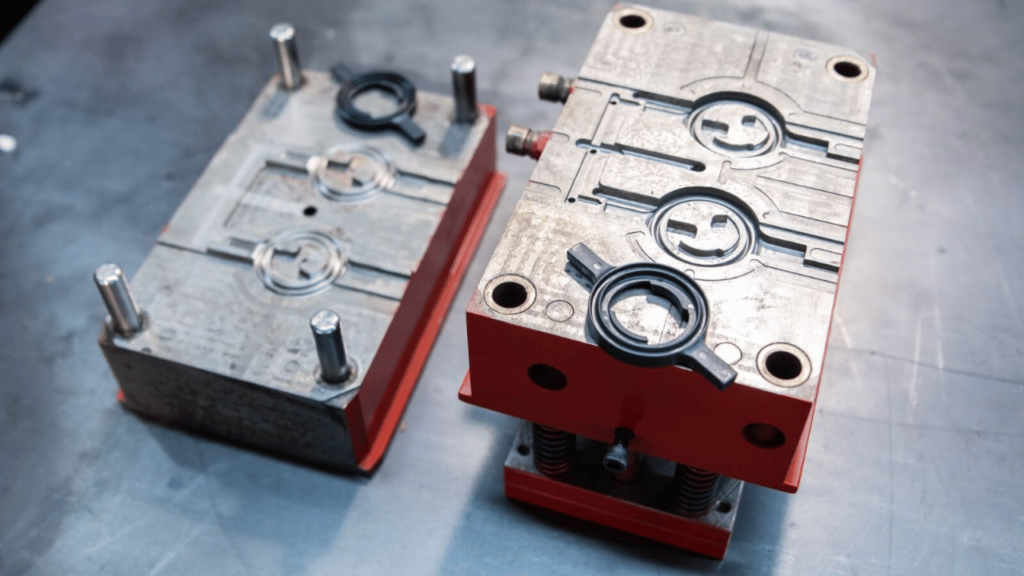
Prototype Molding
Create functional prototypes closely resembling the final product for comprehensive design and functionality testing. Our prototype molds, made from aluminum or steel, cater to varying complexity and volume needs, ensuring cost-effectiveness and durability.
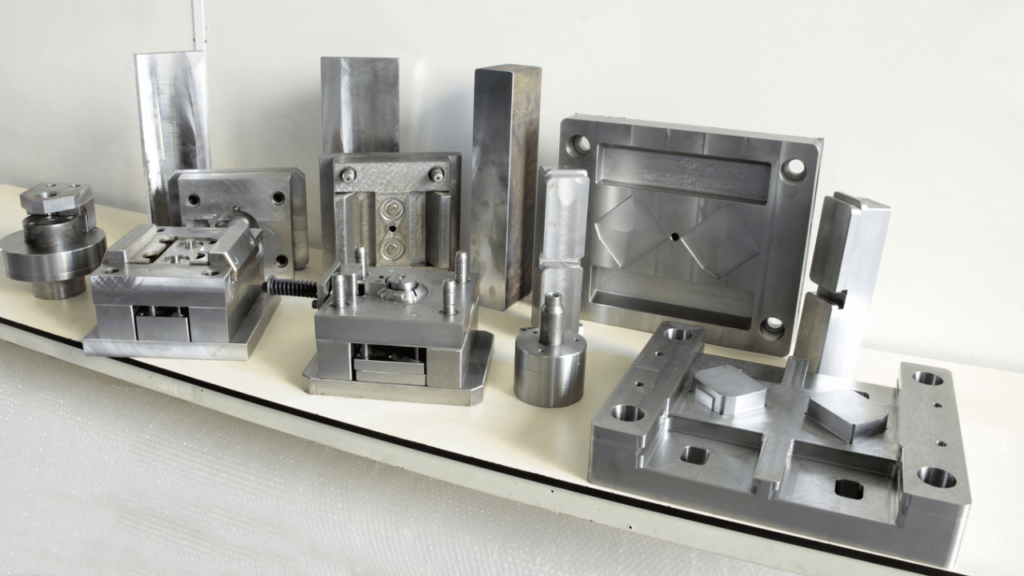
Bridge Molding
Bridge the gap between prototypes and production molds with our temporary bridge molds. Designed for medium-volume production runs while final molds are being built, these steel molds offer a balance between cost, turnaround time, and durability.
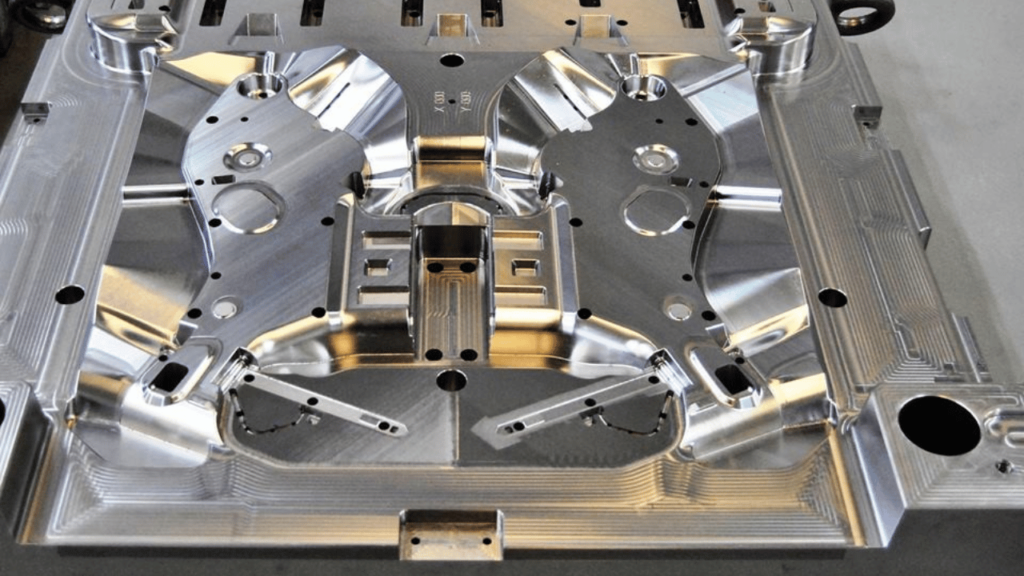
Production Molding
For high-volume production runs, our high-durability steel molds ensure consistent quality and part repeatability. With precision engineering and superior durability, our production molds are designed to meet demanding production requirements.
Get Your Quote Now
- Instant Quotation
- On-Time Delivery
- Affordable Cost
Advanced Capabilities & Applications
Advanced Machinery and Diverse Material Capabilities for Exceptional Outcomes
At Frigate, we harness cutting-edge Toshiba and STM machines, ranging from 100 to 775 tons, to ensure precise and efficient manufacturing processes. Our state-of-the-art equipment empowers us to work with a diverse array of materials, including Nylon, ABS, Polycarbonate, and engineering-grade polymers, among others.
Whether it’s small medical inserts or large automotive and defense parts, our machinery and material capabilities enable us to cater to a wide range of needs. We specialize in engineering-grade polymers, utilizing advanced techniques to achieve intricate shapes and contours with precision.
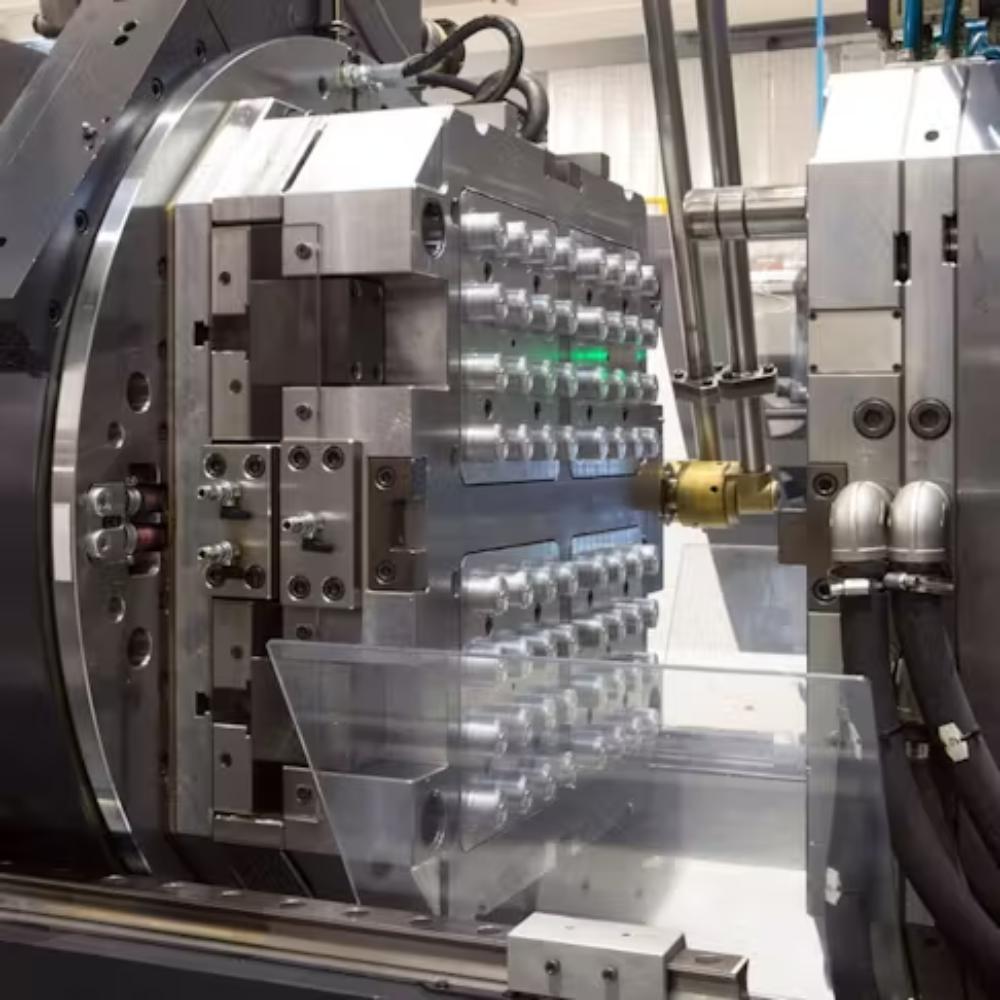
Our Business Verticals
Automotive Parts Manufacturing
Consumer Electronics
Medical Device Industry
Packaging and Containers
Construction Materials
Aerospace Components
Household Goods and Appliances
Toys and Games
Injection Molding Process
Our injection molding process begins with meticulous material preparation, followed by melting and injection into precision-crafted molds made from steel or aluminum. As the molten plastic cools and solidifies, it takes the shape of the desired part. Throughout this streamlined process, we uphold strict quality control measures to ensure each component meets our high standards for accuracy and durability.
After thorough inspection, the finished parts are expertly packaged and delivered to our clients, guaranteeing reliable and timely service.
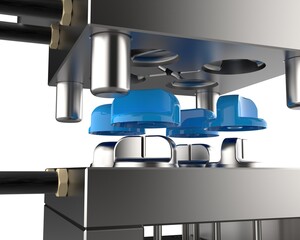
Leverage Our Injection Molding Expertise for Flawless Part Production
At Frigate, we go beyond simply quoting your project. Our certified injection molding experts meticulously review your drawing and 3D files. We then engage in a collaborative consultation to ensure your design specifications translate perfectly into high-quality, functional parts. We analyze your design for optimal production and part quality, including,
- Machinability (part size, tolerances)
- Material selection
- Functionality (surface finishes, draft angles)
- Cost-effectiveness (undercuts, wall thickness, radii)
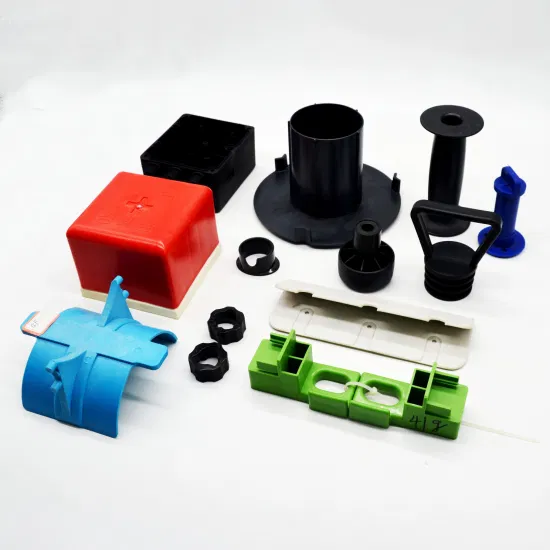
Versatile Materials for Superior Moulding
At Frigate, we utilize a diverse range of materials to meet the unique needs of our clients,
- Noril 30% GF
- Nylon 30% GF
- ABS
- Polycarbonate
- Nylon 66
- Engineering
- Grade Polymers
With our expertise in injection molding, we can mold a variety of products and parts, ranging from small medical inserts to large automotive and defense components.
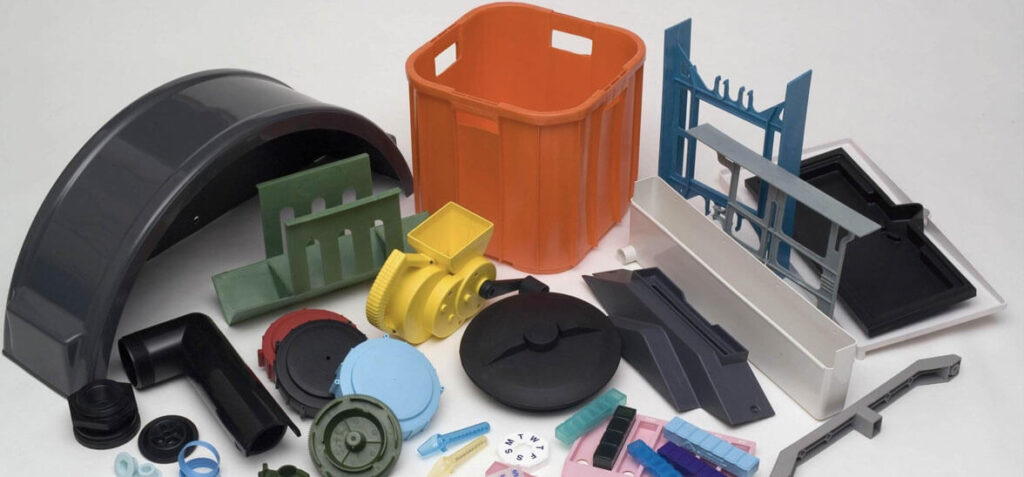
Injection Molding Materials
Dive into the realm of injection molding, where molten polymers take shape with precision and speed. With state-of-the-art technology and expert craftsmanship, we turn raw materials into finished products with unmatched efficiency and quality. Experience the power of injection molding and unlock endless possibilities for your manufacturing needs.
Rigid Plastic Materials
ABS (acrylonitrile butadiene styrene)
High-strength general-purpose engineering plastic, used for many commercial products.
CNC Machining Copper Alloys
Copper 101
Copper C110
CNC Machining Bronze Alloys
Copper C932
CNC Machining Brass Alloys
Copper 260
Copper 360
CNC Machining Stainless Steel Alloys
Nitronic 60 (218 SS)
Stainless Steel 15-5
Stainless Steel 17-4
Stainless Steel 18-8
Stainless Steel 303
Stainless Steel 316/316L
Stainless Steel 416
Stainless Steel 410
Stainless Steel 420
Stainless Steel 440C
CNC Machining Steel Alloys
Steel 1018
Steel 1215
Steel 4130
Steel 4140
Steel 4140PH
Steel 4340
A2 Tool Steel
O1 Tool Steel
CNC Machining Titanium Alloys
Titanium (Grade 2)
Titanium (Grade 5)
CNC Machining Zinc Alloys
Zinc Alloy
Plastic CNC Machining Materials
ABS
High-strength engineering plastic used for many commercial products.
Acrylic
A clear glass-like plastic. Good wear and tear properties. Great for outdoor use.
Delrin (Acetal)
Acetal
Delrin 150
Delrin 100
Resin with good moisture resistance, high wear resistance, and low friction.
Garolite
Garolite G10 (FR4)
Garolite G10 (non-FR)
Garolite G11 (FR5)
Constructed of an epoxy resin with fiberglass fabric reinforcement, also called epoxy-grade industrial laminate and phenolic, this material offers high strength and low moisture absorption.
HDPE
High-density polyethylene is a moisture and chemical-resistant plastic with good impact strength. The material is outstanding for outdoor applications as well as watertight containers or seals.
Nylon 6/6
Offers increased mechanical strength, rigidity, good stability under heat and/or chemical resistance.
PC (Polycarbonate)
With almost twice the tensile strength of ABS, polycarbonate has superior mechanical and structural properties. Used widely in automotive, aerospace, and other applications that require durability and stability.
PEEK
PEEK
PEEK (USP Class VI TECAPEEK)
PEEK GF30
Offering excellent tensile strength, PEEK is often used as a lightweight substitute for metal parts in high-temperature, high-stress applications. PEEK resists chemicals, wear, and moisture.
Polypropylene
Has excellent electrical properties and little or no moisture absorption. It carries light loads for a long period in widely varying temperatures. It can be machined into parts requiring chemical or corrosion resistance.
PTFE (Teflon)
This material surpasses most plastics when it comes to chemical resistance and performance in extreme temperatures. It resists most solvents and is an excellent electrical insulator.
UHMW PE
Ultra-high molecular weight polyethylene. A general-purpose material. It offers a unique combination of wear and corrosion resistance, low surface friction, high impact strength, high chemical resistance, and does not absorb moisture.
PVC
Polyvinyl chloride (Type 1) is a highly chemical-resistant synthetic plastic, PVC is commonly in environments exposed to liquids or requires electrical insulation.
ULTEM
ULTEM 1000
ULTEM 2300
ULTEM (Polyetherimide) is a stiff, robust, performance-grade thermoplastic that can operate continuously in high-temperature environments (up to 340°F). It has one of the highest dielectric strengths of commercially available thermoplastics, making it an excellent electric insulator. Since ULTEM is also resistant to chemicals, easily cleaned, and does not absorb moisture, it is often used for medical applications.
CNC Machining Finishes
Standard (As-Milled)
The finish option with the quickest turnaround. Machined parts are left with visible tool marks and potentially sharp edges and burrs, which can be removed upon request. CNC machining surface finish is comparable to 125 uin Ra finish.
Bead Blast
The part surface is left with a smooth, matte appearance.
Tumbled
This is a batch-based process that tumbles vibrating media to remove sharp edges and burrs on CNC parts. Tumbling can remove machine marks on exterior surfaces. Parts over 8” may require a manual review.
Anodized (Type II Or Type III)
Type II (MIL-A-8625, Type II) creates a corrosion-resistant finish. Parts can be anodized in different colors—clear, black, red, and gold are most common—and are usually associated with aluminum. Type III (MIL-A-8625, Type III, Class 1/2 “hardcoat”) is thicker and creates a wear-resistant layer in addition to the corrosion resistance seen with Type II.
Titanium Anodize
A surface finish for titanium per AMS-2488 Type 2 specification. Also called Tiodize, this finish increases fatigue strength and the wear resistance of a part. Titanium anodized parts are common in aerospace and medical device manufacturing. Non-pigmented titanium anodize finishes will dull shine.
PTFE Impregnated Hard Anodize
A hard coat anodize process that embeds PTFE to create a self-lubricating, dry contact surface with Type 3 hard coat’s protective properties. This finish can be used on aluminum alloys or titanium and increases the service life of the product. This finish conforms to the AMS-2482 Type 1 Hard Coat Anodizing with Teflon (Non-Dyed).
Chem Film (Chromate Conversion Coating)
Provides corrosion resistance and good conductivity properties. Can be used as a base for paint. Can leave surface yellow/gold. Adds very little thickness, about 0.00001”-0.00004”. Chem film will conform to MIL-DTL-5541, TYPE I/II.
Passivation
Improves corrosion resistance for 200 and 300 series and precipitation hardened corrosion-resistant steels. Thickness is negligible, about 0.0000001”. Conforms to ASTM A967, AMS-QQ-P-35, MIL-STD-171, ASTM A380, or AMS 2700.
Powder Coat
This process is where powdered paint is sprayed onto a part and baked in an oven. This creates a strong, wear- and corrosion-resistant, more durable layer than standard painting methods. A wide variety of colors are available to create the desired aesthetic.
Electropolishing
An electrochemical process cleans steel parts to reduce corrosion and improve appearance, by making the metal brighter. Removes about 0.0001”-0.0025” of the metal. Conforms to ASTM B912-02.
Electroless Nickel Plating
Provides uniform nickel coating which offers protection from corrosion, oxidation, and wear on irregular surfaces. The finished part will be brighter. Thickness starts at .0001”. Conforms to MIL-C-26074.
Silver Plating
Silver offers high solderability and electrical conductivity but is susceptible to tarnish. Conforms to AMS QQ-S-365D. Thickness is about 0.00002” – 0.0003.”
Gold Plating
Gold Plating provides good corrosion and tarnish resistance with excellent solderability. Default application specification is MIL-G-45204 and ASTM B488, CLASS 00, 0, OR 1. Thickness is about 0.00002″ – 0.00005.”
Zinc Plating
Provides uniform zinc coating which offers protection from corrosion, oxidation, and wear on irregular surfaces. Conforms to ASTM B633-15.
Frigate Approach
Why choose Frigate?
Experience precision, reliability, and efficiency with Frigate’s injection molding services. Trust us to deliver superior quality components tailored to your specifications, from material selection to final delivery. Contact us today to discuss your project needs and discover how Frigate can support your manufacturing requirements with excellence.
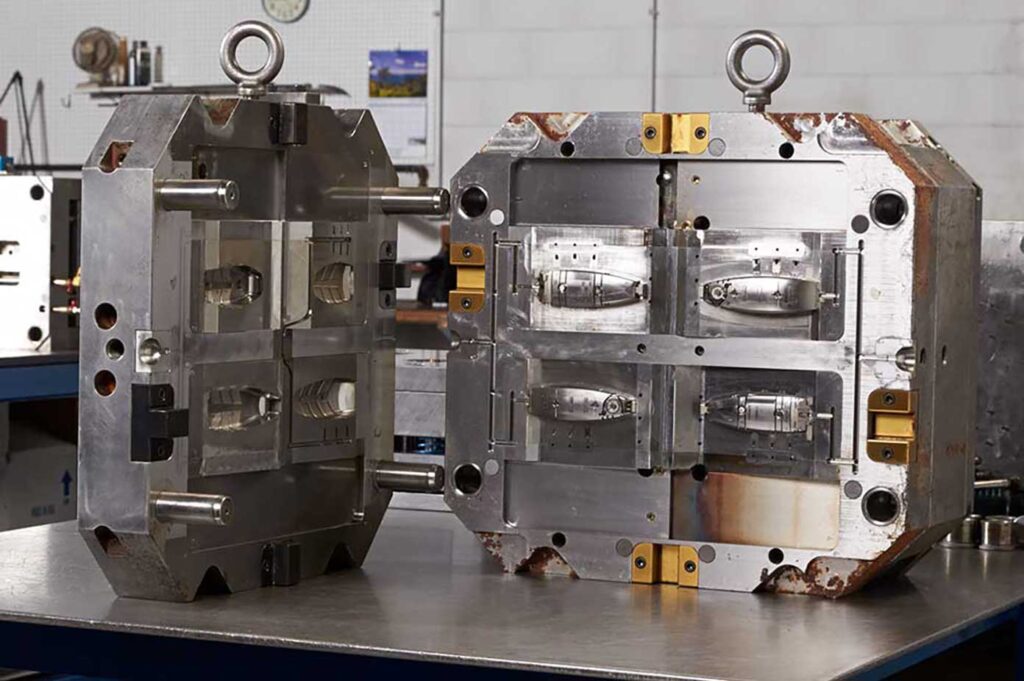
What Our Customers Say about Frigate
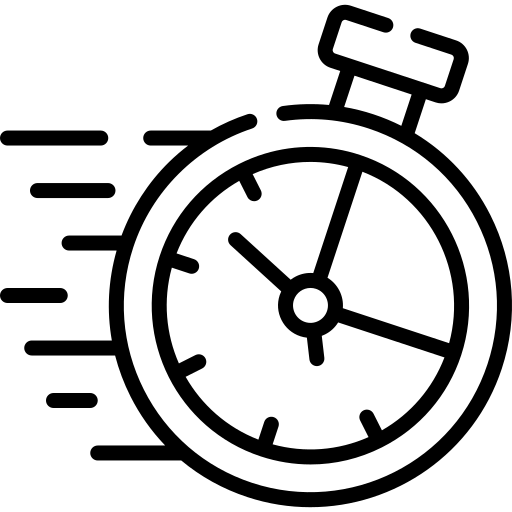
21%
Faster Manufacturing
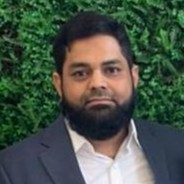
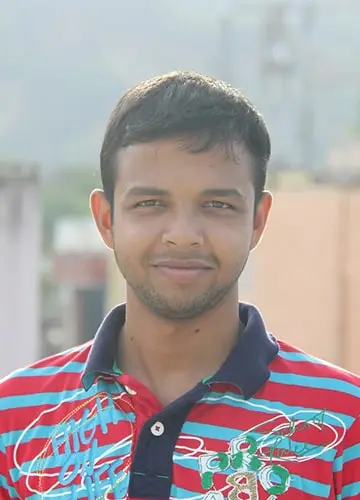
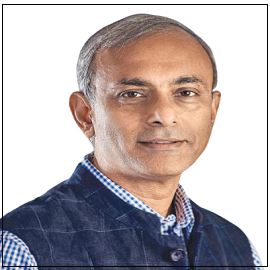
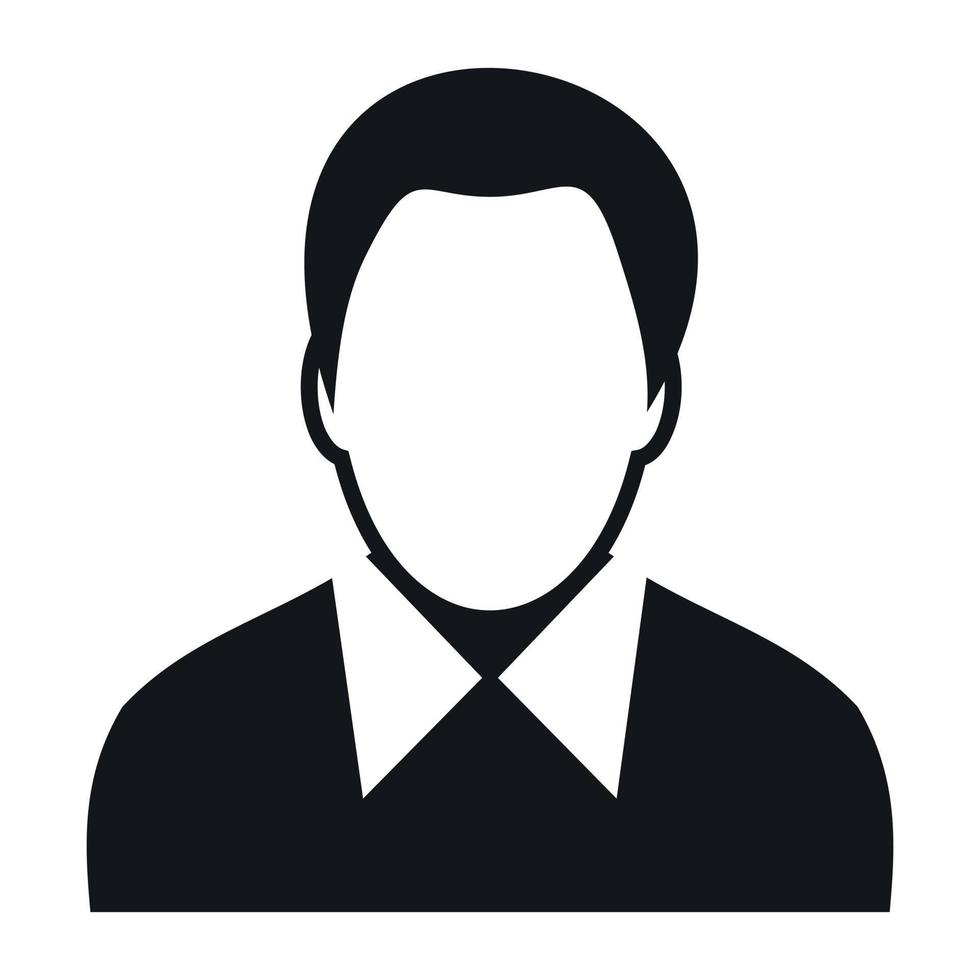
Having Doubts? Our FAQ
Check all our Frequently Asked Question
Which Molding Process Is Best?
There are three primary procedures to consider when plastic injection molding: hybrid, electric, and hydraulic. Speak with a qualified engineer for advice on the best course of action for your project.
How to Figure Out the Volume Needs?
Let Frigate help you determine the volume of your project. Our plant specializes in low, intermediate, and high-volume injection molding to meet the demands of different projects.
How Much Does the Process Cost?
Since precise molds are the main manufacturing expense, it is imperative to invest in high-quality steel molds. Frigate guarantees long-lasting molds that provide great return on investment.
How can I reduce mold costs?
- Eliminate Undercuts.
- Simplify Features.
- Employ Core Cavity Approach.
- Minimize Cosmetic Finishes.
- Design Self-Mating Parts.
- Optimize Mold Reuse.
- Prioritize DFM Analysis.
- Utilize Multi-Cavity Molds.
- Assess Part Size.
Optimize your mold costs with these strategic approaches for efficient and cost-effective production.
Manufacturing Capacity
Ferrous casting
Mold size(max): 1m X 1m
Weight Range: 1 KG ~ 30 KGS
Mold size(max): 1.5m X 1.5m
Weight Range: 30 KG ~ 150 KGS
Mold size(max): 3m X 3m
Weight Range: 100 KG ~ 1000 KGS
Mold size(max): 500 MM X 500 MM
Weight Range: 0.250 KG ~ 20 KGS
Mold size(max): 500 MM X 500 MM
Weight Range: 0.100 KG X 20 KGS
Non-ferrous casting
Capacity: 5000 MT/a
Range of weight: 100 gm to 20 KGS
Mold size(max): 1 M X 1 M
Weight Range: 0.5 KG X 50 KGS
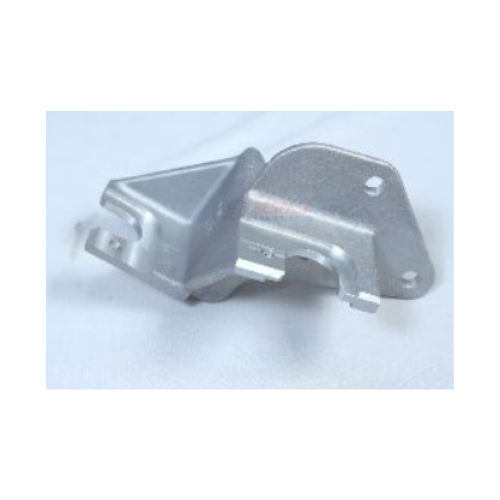
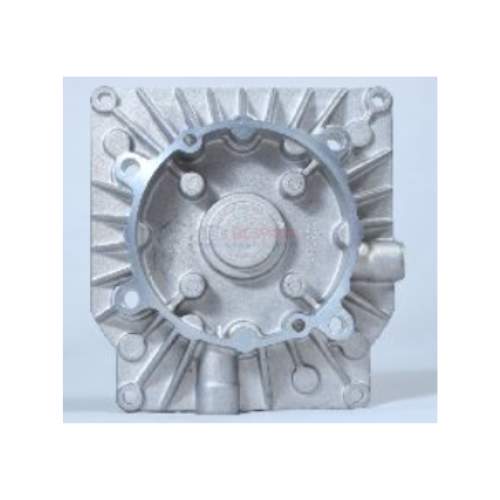
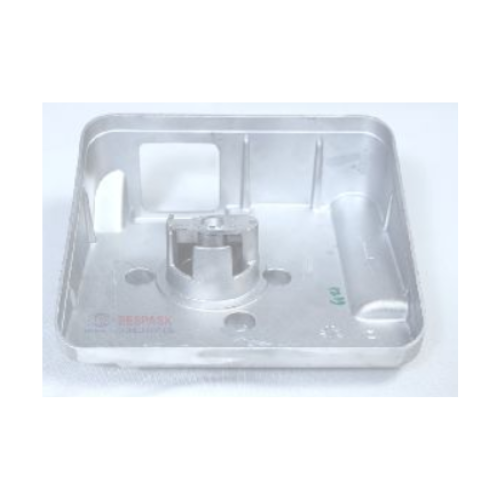
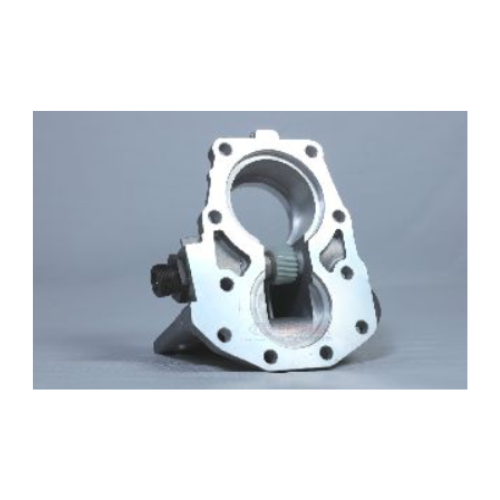
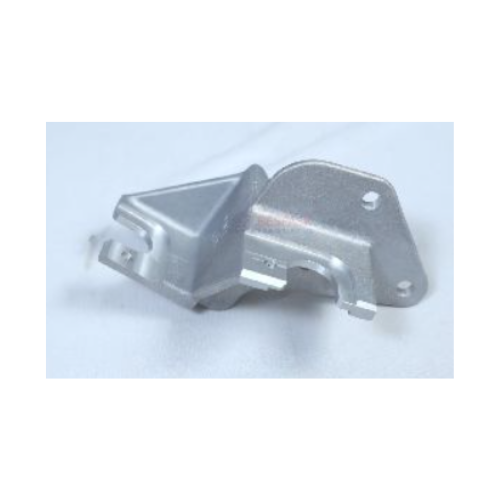
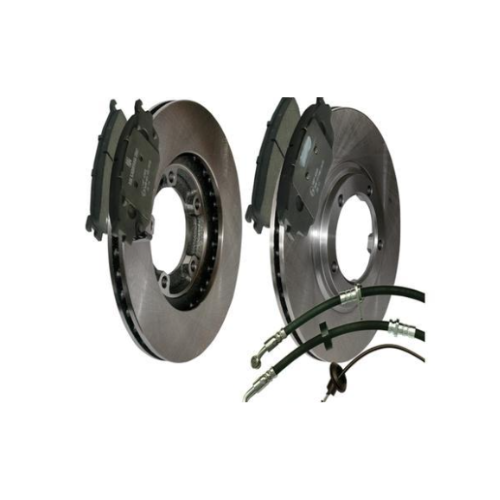
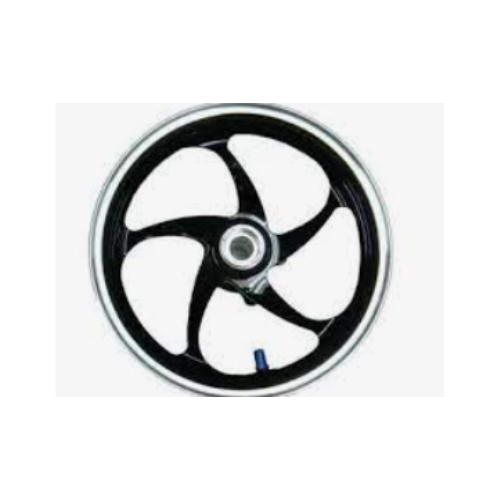
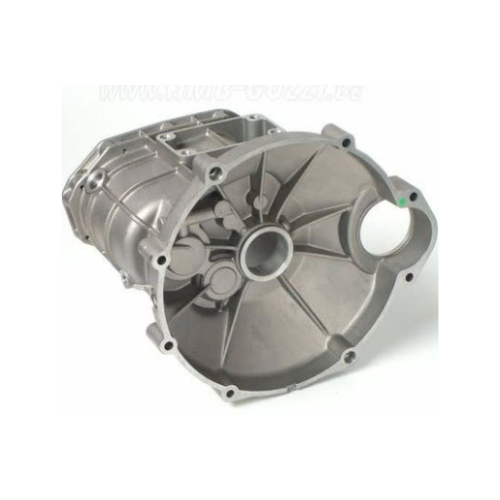
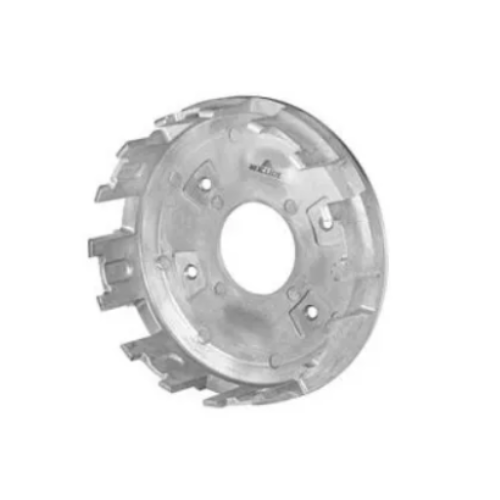
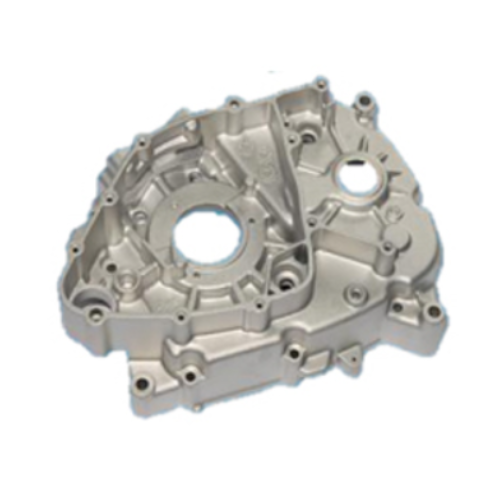
Forging
Capacity: 20,000 Tons per Annum
Range of weight: 300 KG to 1 Ton
Hammering: 5 Ton
Range of weight: 0.2 KG to 200 KGS
Hammering: 1600 Ton Hydraulic press
Ring size: 350 MM OD to 3000 MM OD
Range of weight: 15 KGS to 3200 KGS
Materials
Carbon Steel, Stainless Steel (AUSTENITE), Alloy Steel, Stainless Steel (MARTENSITE), etc.
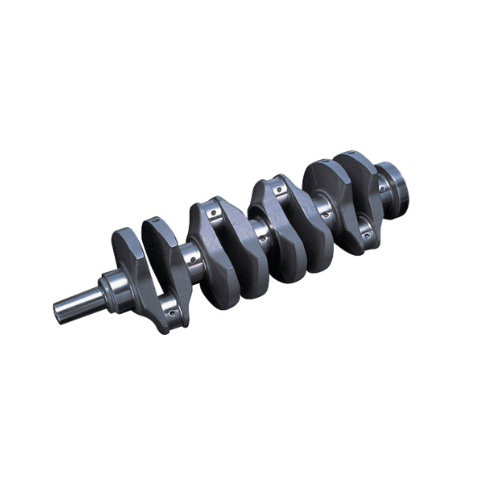
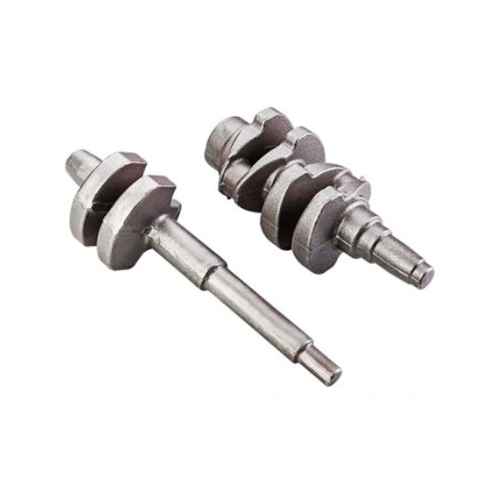
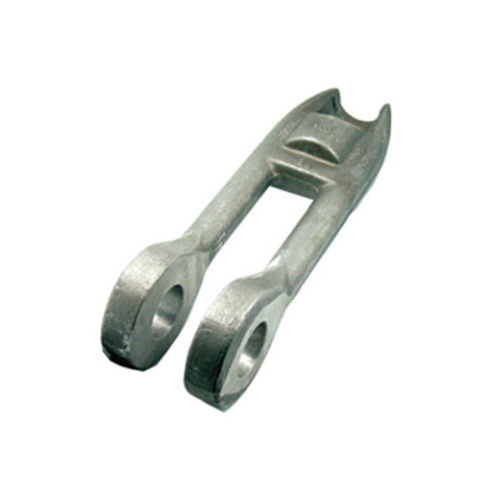
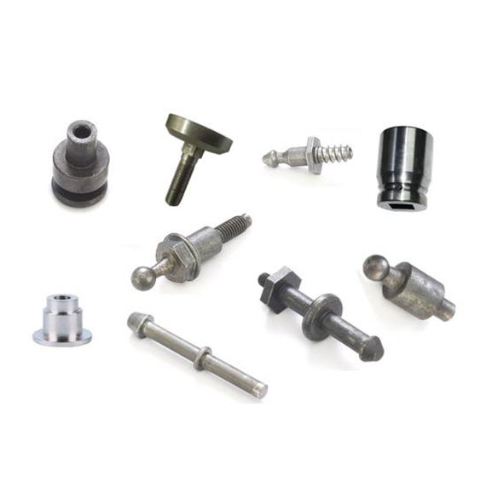
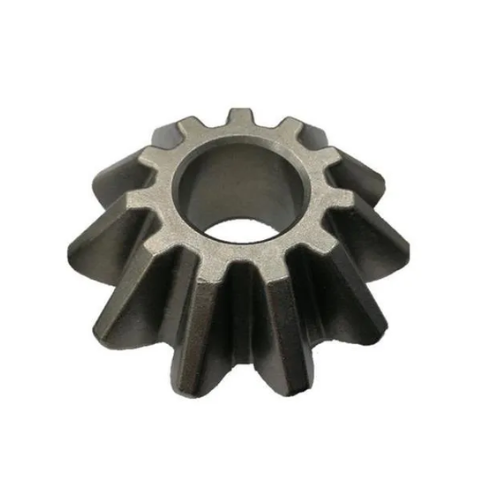

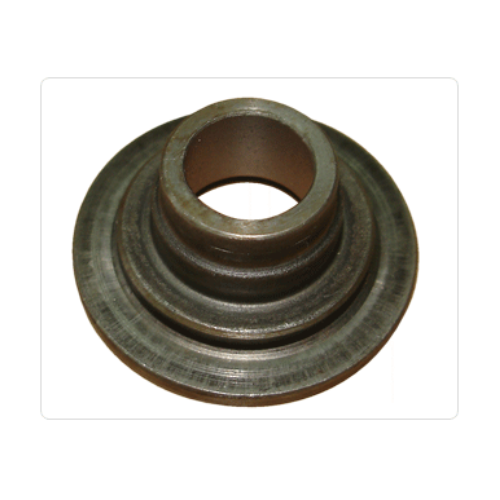
Machining
Materials
Steel, Aluminum, Brass, Copper, Titanium, Nickel Alloys, Tungsten Carbide, etc.
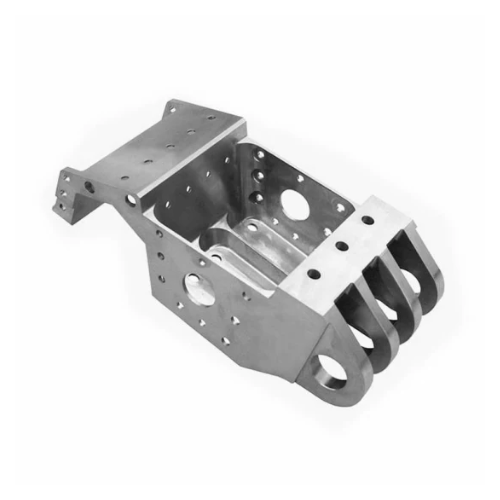
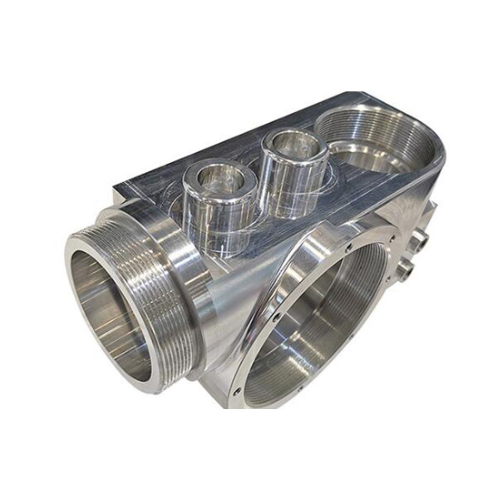
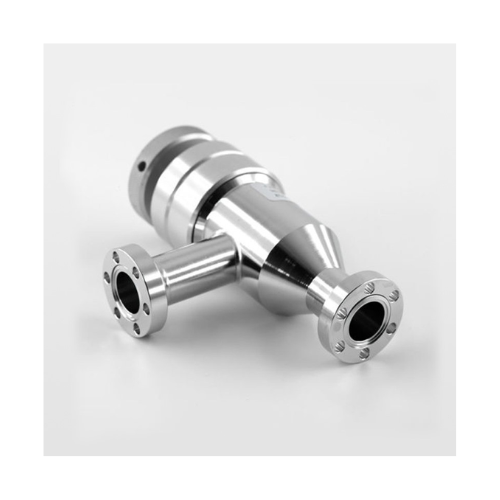
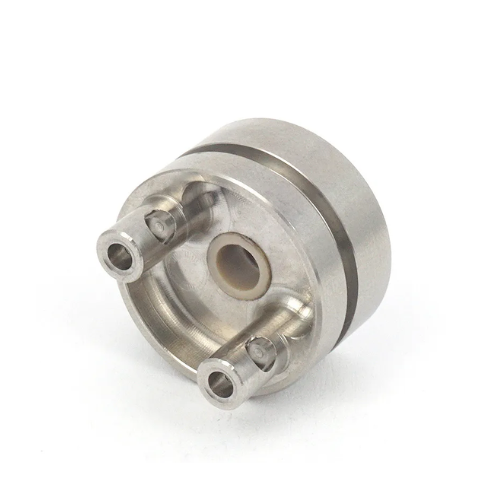
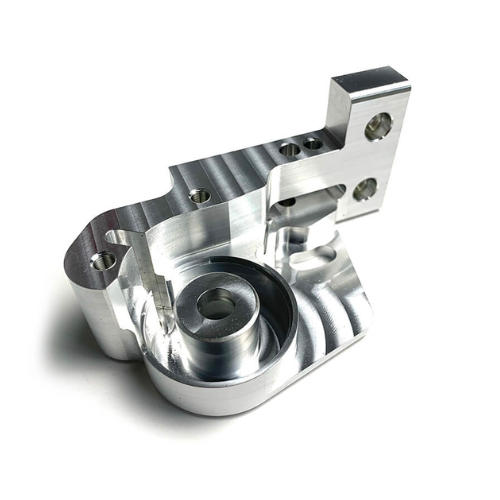
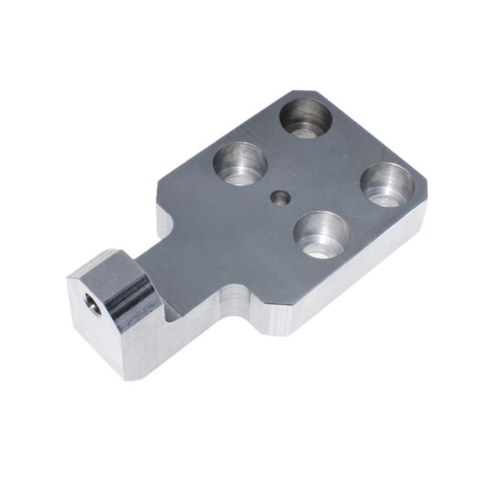
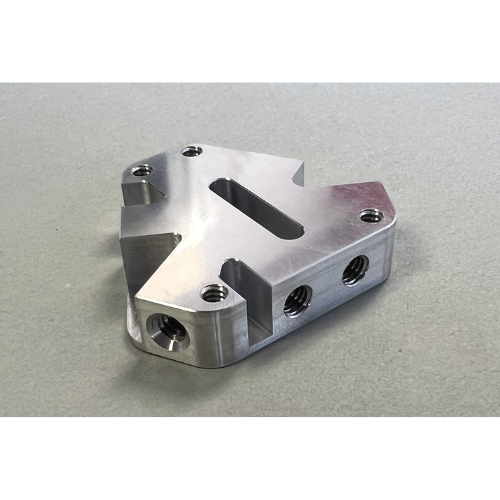
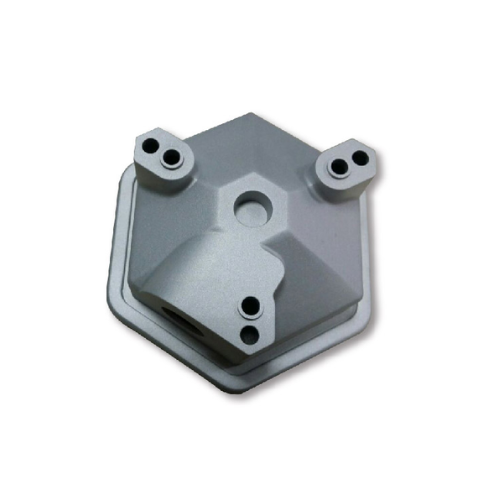
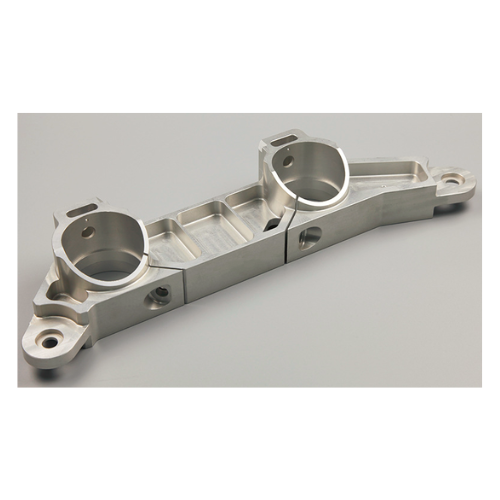
Plastics
1250 X 1250 MM
Within 10 microns
Materials
Engineering Plastics, Polyethylene, Polypropylene, Polyvinyl chloride, Polyethylene terephthalate, Bioplastics, etc.
Rubber
Materials
Natural rubber, Styrene-Butadiene Rubber, Nitrile Butadiene Rubber, Silicone Rubber, Fluorocarbon Rubber, Recycled Rubber, etc.
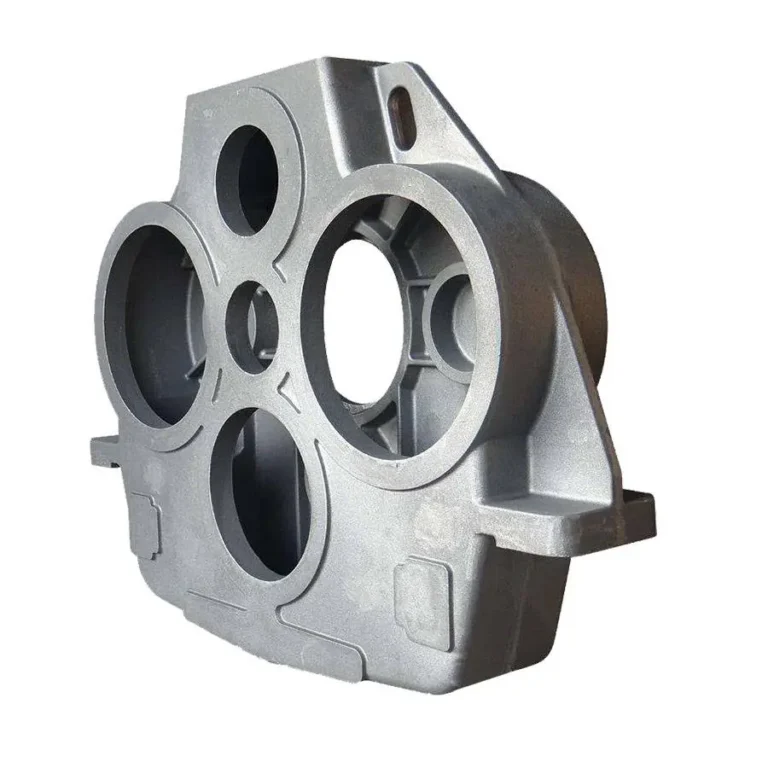
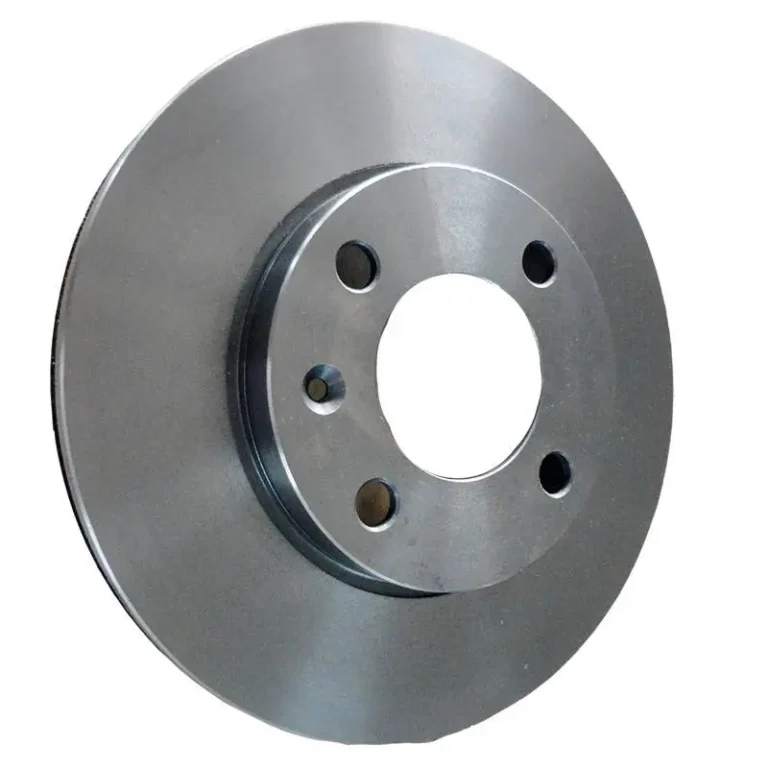
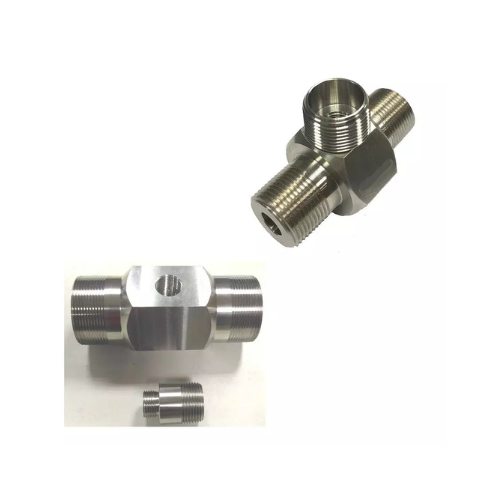
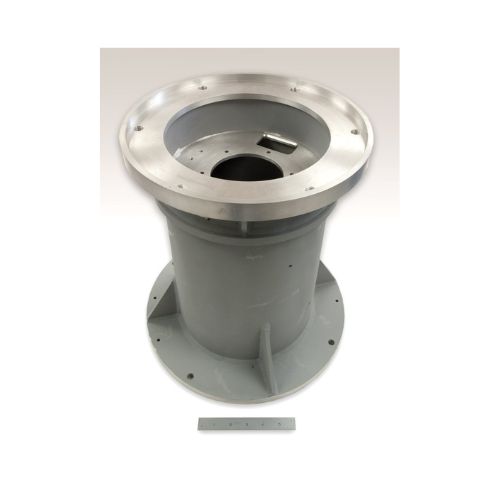
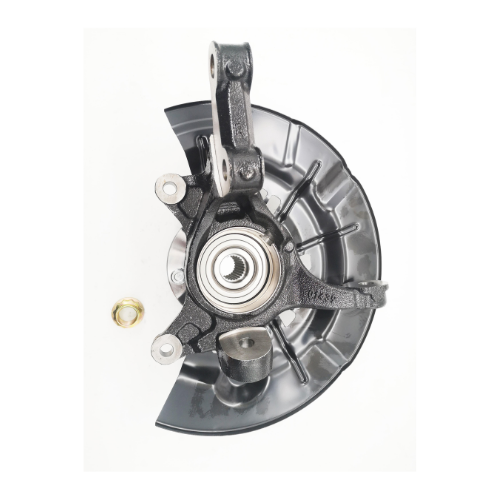
Sheet Metal Fabrication
Sheet Thickness
Materials
Mild Steel, Stainless Steel, Aluminum, Brass, Copper, etc.
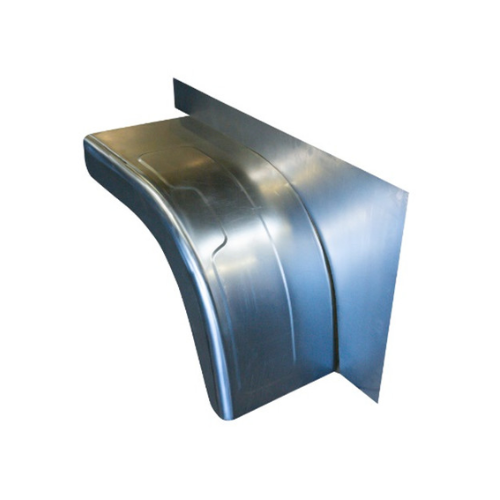
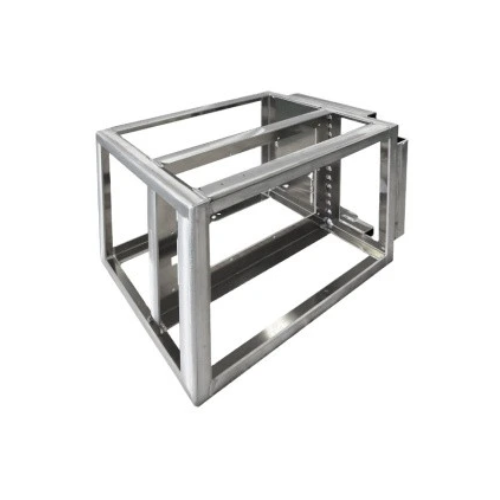
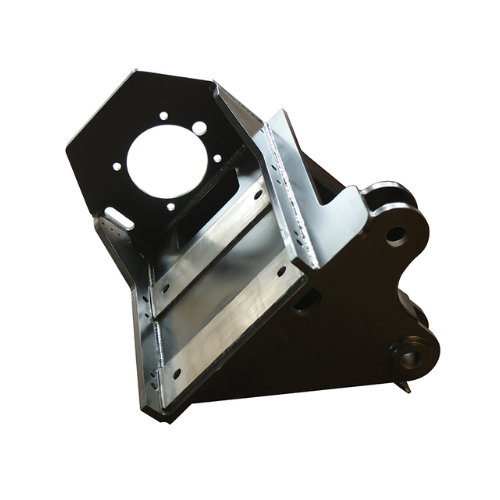
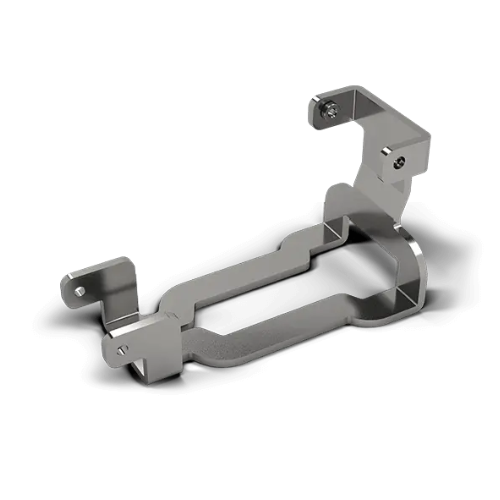
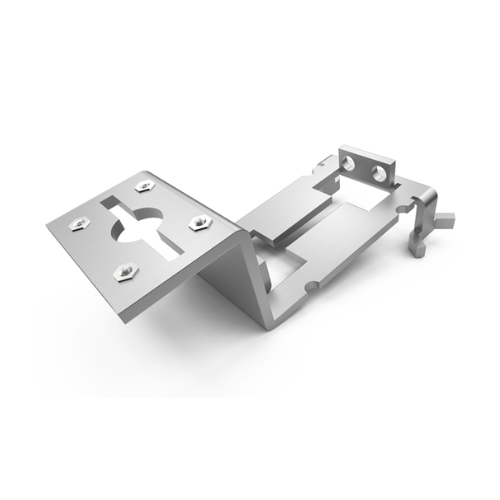
We'd love to Manufacture for you!
Submit the form below and our representative will be in touch shortly.
LOCATIONS
Global Sales Office
818, Preakness lane, Coppell, Texas, USA – 75019
Registered Office
23, 6th West Street, Balaji Nagar, Kattur, Pappakuruchi, Tiruchirappalli-620019, Tamil Nadu, India.
Operations Office
9/1, Poonthottam Nagar, Ramanandha Nagar, Saravanampatti, Coimbatore-641035, Tamil Nadu, India. ㅤ